Smart ESM MEPC.259(68) Exhaust gas wash water monitoring system - Overview
Rivertrace's MEPC.259(68) compliant exhaust gas scrubber wash water monitoring solution. What is it and what does it do?
Context
The 2020 Sulphur cap
The 2020 sulphur cap is a global regulation that limits the amount of sulphur in ships' fuel. The IMO (International Maritime Organization) introduced the cap on January 1, 2020.
- The cap limits the sulphur content of ships' fuel to 0.5%
- This is down from the previous limit of 3.5%
- The cap applies to all ships outside of certain designated Emission Control Areas (ECAs)
- In ECAs, the limit is already 0.10%
- In ECAs, the limit is already 0.10%
- To reduce air pollution and protect health and the environment.
- Burn distillates
- Burn hybrids or blends
- Install Exhaust Gas Cleaning Systems (EGCS) <-- This is where we help!
- Burn LNG
- Use other alternative sources
- Switch to sulphur-free HVO fuel
What is an exhaust gas cleaning system? (EGCS) - AKA Scrubber
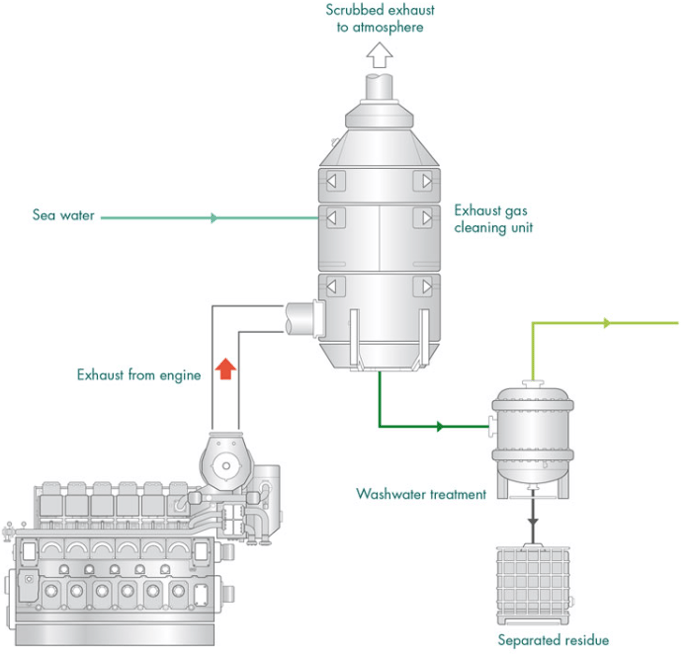
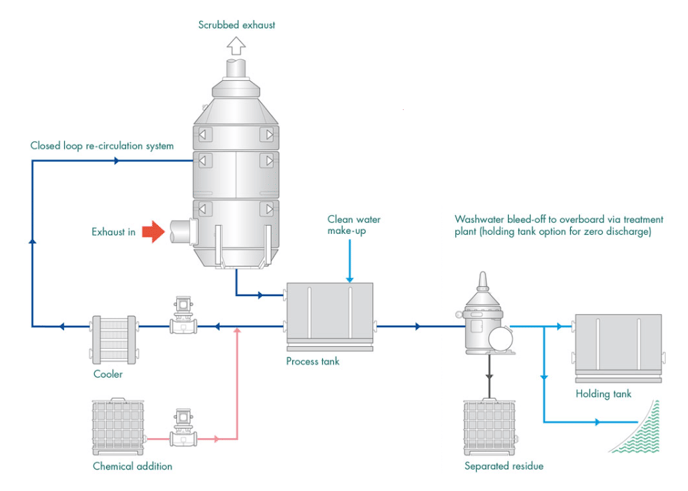
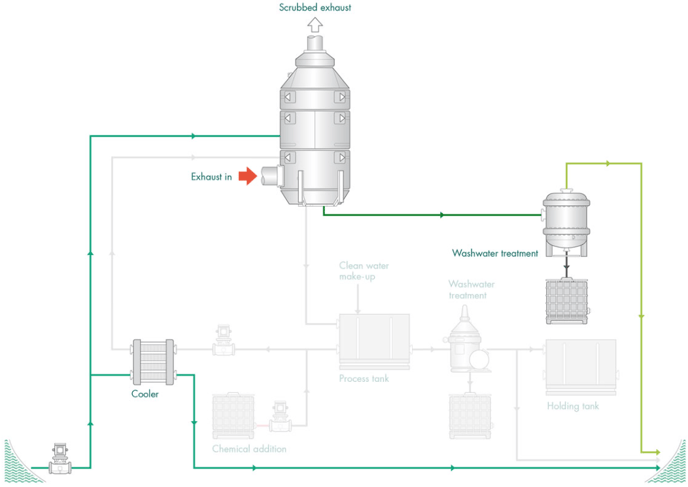
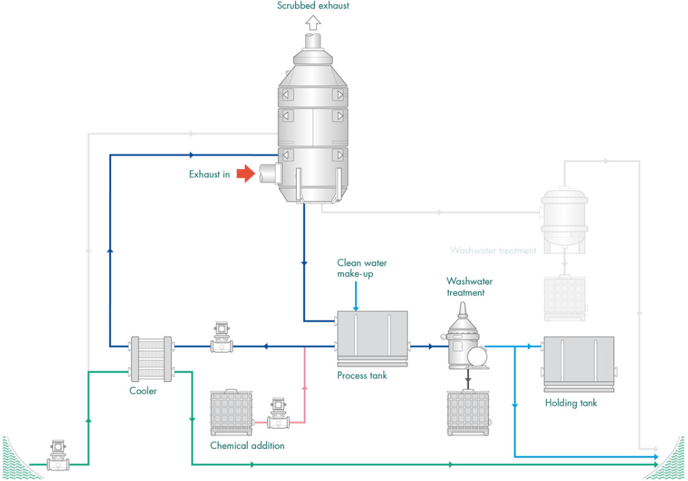
Introduction to the Smart ESM.
The SMART ESM has been developed in line with MEPC.259(68) guidelines for exhaust gas cleaning systems for washwater monitoring.
The system is used to measure contaminants within exhaust gas scrubber wash water before being discharged to sea. The SMART ESM is a side stream monitor continuously measuring the following parameters:
- Polycyclic Aromatic Hydrocarbons (PAH)
- pH
- Temperature
- turbidity
The unit is suitable for inlet and outlet monitoring of the Exhaust Gas Cleaning System (EGCS).
The Smart ESM accurately measures the sample and sends the measured values to the exhaust gas cleaning system control module via Modbus over RS485 or through conventional 4-20mA signals. This makes integration and retrofitting this system very simple.
The Smart ESM does not have any direct control over the scrubber system. This remains the responsibility of the exhaust gas cleaning system manufacturer. The smart ESM is, however responsible for accurate reporting these measured values.
Due to the very aggressive nature of exhaust gas scrubber wash water, very careful consideration to materials and design has been essential to ensure that the Smart ESM is robust and reliable in the field.
Smart ESM Overview
The Smart ESM is system is made up of two key modules, the analysing and control module and sample pump module.
The analysing and control houses sample conditioning equipment, customer terminations, analysing components and the control computer module.
Sampling
Some vessels can have up to three Smart ESM systems onboard, working on one scrubber system. This is typically open loop of hybrid system that are required to measure how much contamination the scrubber system has added to the sea water that is being used.
In these cases, sampling is carried out at the points marked below:
A - This is the clean seawater in, before being passed over exhaust gases. This is effectively the baseline.
B - This is the sea water once it has passed the exhaust gases and usually at its dirtiest. This measurement is usually used by the scrubber control system to determine how to process the wash water . It also allows the scrubber control system to check the efficiency of their scrubbing unit.
C - Post treatment. This point checks that the water has been processed correctly and that the water is returned to the ocean in a fit state.
The Exhaust gas cleaning system will check the measured values obtained at point "C" against the measured values obtained at point "A". Under MEPC regulation, the exhaust has cleaning system is only allowed to increase the Turbidity, pH, PaH content and temperature of the wash water by predetermined quantities. These allowable quantities depend on the size of the ships engine.
Analysing and control module
Sample pump module
Key components explained
Computer Module
Controls the entire Smart ESM system. This module houses the display and all customer IO.
Measuring Cell
The measuring cell houses all measuring devices. This includes PaH Cassette, pH probe, turbidity cassette and Thermistor. The sample passes through the measuring cell where it passes the analysing equipment. The PaH, Turbidity and temperature sensors are isolated from the sample and the pH probe is submerged within the sample.
Both IR Turbidity and UV PaH cassettes slide into the cell assembly on specially designed runners that allow automatic alignment to the measuring tube. The cell can be used with one cassette, two cassettes or no cassettes installed and the computer control module will automatically detect what is installed, before displaying its measured value.
Autoclean actuator
The Smart ESM uses a pneumatic autoclean actuator to ensure that the glass sampling tube within the measuring cell is kept clean. this is only required when cassettes are installed as the pH probe and thermistor do not depend on optically clear glass for accurate measurement to take place.
PaH Measuring cassette
The PaH Cassette is designed to detect polycyclic aromatic hydrocarbons (PaH) in water. The cassette uses a 254nm excitation wavelength to excite the particles of PaH within the sample. Detectors will receive the emitted light from the sample through dielectric filters before quantifying this light and determining the PaH content within the sample.
The PaH Cassette operates on 48V DC and communicates with the control computer module via RS485.
The PaH Cassette is a calibrated part.
The PaH Cassette should be verified onboard every 6 months and replaced every 24 months. A warning message will be displayed as the computer control module 2 weeks before the replacement of the cassette is due, allowing time for a spare part to be obtained.
Turbidity cassette
The IR turbidity cassette uses Infrared light scatter to determine the turbidity of the sample, inline with ISO standards.
The IR Turbidity Cassette operates on 48V DC and communicates with the control computer module via RS485.
The IR turbidity Cassette is a calibrated part.
The IR turbidity Cassette should be verified onboard every 6 months and replaced every 24 months. A warning message will be displayed as the computer control module 2 weeks before the replacement of the cassette is due, allowing time for a spare part to be obtained.
Sample flow switch
A sample flow switch is fitted to ensure a live sample is always monitored. Logic within the Computer control module checks that when the scrubber system is active, the flow switch is also receiving flow. If there is a mismatch between scrubber state and flow switch status, a warning message will be displayed.
A flow rate of 0.8LPM is necessary to throw the flow switch.
Sample / Clean valve
The sample / clean valve is controlled by the Smart ESM control module and will automatically actuate when a flushing or cleaning process is underway. The valve is a "T" port valve, meaning when clean water is selected, all ports will be common, allowing clean water to flush the Smart ESM Measuring cell as well as the sample line, back to the scrubber system.
Debubbler
Due to the nature of exhaust gas scrubber wash water, a debubbler is necessary to remove the majority of air that is present within the sample. The device uses gravity to separate air from sample and vents excess air through a float type valve at the top of the cylinder. This part is largely maintenance free but cleaning should take place periodically.
Never use alcohol or other chemicals to clean the debubbler. Use only a mild detergent.
Sample pump
The sample pump is designed to increase sample pressure and homogenise the sample to give a more accurate measurement. Higher sample pressure also compresses air and also results in a higher accuracy due to the air having less impact on the optical analysis of the sample.
System Specifications:
Number of sample points |
1 analyser per sample point with optional measurement parameters |
PAH Range |
0μg/L to 4500μg/L |
PAH Accuracy |
5% of measurement reading |
PaH Measurement Principle |
UV Fluorescence |
Turbidity Range |
0 – 500 NTU |
Turbidity Accuracy |
0.1NTU up to 100 NTU, 1NTU thereafter. |
Turbidity Measurement Principle |
IR Scattering |
pH Range |
0 – 14 pH |
pH Accuracy |
0.1 pH |
pH Measurement Principle |
pH Electrode |
Approval |
DNV-GL Certificate of Conformity |
IP Rating |
IP66 |
Supply Voltage |
230VAC 50/60 Hz |
Outputs |
4-20mA for each Parameter Modbus |
Wetted Parts materials |
Stainless Steel, Glass, PVC-u, Acetal, Nylon, Polymer Type 12, Delrin, Acrylic tube |
Automatic cleaning device fitted as standard |
YES |
Optimum Air pressure |
6 BAR |
Compressed Air normal / average consumption |
450mL / Hr |
Air Regulator included on standard Monitor |
YES |
Flow rate range (Sample / Clean) |
1 to 4 LPM |
Optimum flow rate (Sample / Clean) |
3 LPM |
Ambient Temperature range |
1°C to 50°C |
Sample Temperature range (Sample / Clean) |
1°C to *40°C *Higher optional with a heat exchanger |
Sample pressure range (Sample / Clean) |
1 to 9 Bar *Motor/Pump provided if below 0.5 bar |
Optimum Measuring pressure (Sample / Clean) |
3 Bar |
Air Supply required for Standard Monitor? |
YES |
Air Supply required pressure range |
4 - 10 BAR |
Standard Maintenance schedule
Action |
Frequency |
|||||
1 Month |
3 months |
6 Months |
12 months |
24 Months |
As Needed |
|
Remove and clean the large particle filter. Replace as needed. |
O |
|
|
|
|
O |
Calibrate pH probe using Rivertrace buffer solution |
|
O |
|
|
|
O |
Check PAH and Turbidity parameter accuracy using on-site check kits. |
|
|
O |
O |
||
Replace PAH Cassette |
|
|
|
O |
O |
|
Replace Turbidity Cassette |
|
|
|
O |
O |
|
Replace pH probe |
|
|
|
O |
|
O |
Replacement of Auto clean wiper blade by crew |
|
|
|
O |
|
O |
Replace Desiccator
|
|
|
|
O |
|
O |
Support
Rivertrace offer extensive global support, both onboard and remote to ensure that any queries you may have, regarding your Rivertrace equipment can be answered swiftly, efficiently and most importantly, correctly.
Our ever-growing knowledge base optimises first line support by giving consistent, clear and easy to follow guidance for your Rivertrace products, allowing crew to maintain and repair equipment at any hour of the day (or night) with no time differences or communications lag that is often experienced in global industries.
The Knowledge base articles are searchable, indexed and are continually adapted based of real world feedback.
Created by service engineers across the globe, user friendliness and simplicity has been a key focus here. This means that even end users with limited experience now have access to the same expert advice and useable procedures that were once only held by well seasoned Rivertrace service engineers.
The aim of this is maximum product uptime and shared knowledge throughout our network.
Feedback is very highly valued.
See our Smart ESM Articles here
See our entire knowledge base here